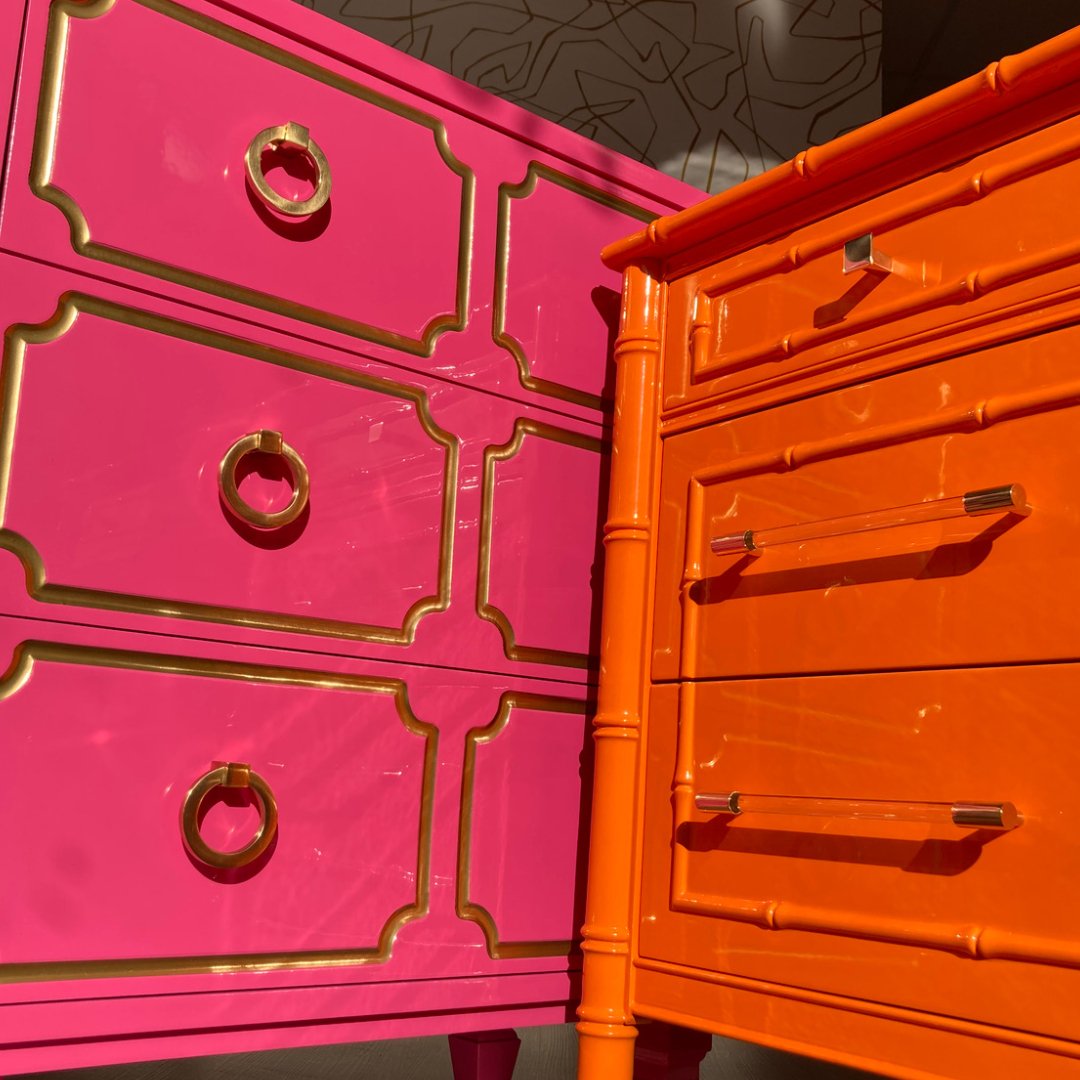
The Secret Tools for Mastering Gorgeous Upcycled Furniture
Share
DISCLOSURE: ALL THE LINKS PROVIDED HERE ARE MATERIALS AND TOOLS THAT WE USE REGULARLY AT CASEY GRACE STUDIOS. PER FEDERAL TRADE COMMISSION (FTC) GUIDELINES I AM REQUIRED TO SHARE THAT THIS ARTICLE CONTAINS AFFILIATE LINKS FOR WHICH I MAY RECEIVE A SMALL COMMISSION.
When I started down this furniture flipping journey, I had a lot to learn. I gleaned a ton of tips from painters I’ve hired in the past (thank you Eric!), as well as some great online sources. But there’s a little set of tips and tricks we've stumbled upon and I’ve never seen anyone else talk about. Perhaps these are little secret gems painters keep to themselves…? In the off chance these are totally new to people, I threw them together into this blog.
In addition to these tools, I must admit I have a secret weapon in my back pocket! Handy Andy! I know he’s been called that before so I’m jumping on the band wagon. When I finally leased space I knew I needed more hands on help. Andy was one of the first that responded and boy did I hit the jackpot!!
Andy spent 20ish years in NYC working on broadway plays. What I mean is, he built them, designed them, managed them, shipped it all to London, or wherever the set for Harry Potter needed to go! He can build or fabricate ANYTHING! I am so eternally grateful for finding him and for his supportive attitude and ideas! I could not say yes fast enough. He’s making my little artist-, designer-, maker-heart so happy every single day!
So, needless to say most of these tips and tricks have come from Andy’s experience and diligence to improve our process.
Many of you probably know now that I use exclusively water-based 2k lacquer. We go to the extra step of 2k which most do not, and we believe whole-heartedly in water-based alternatives. We avoid “paint” products at all costs, as well as anything solvent based. All of that is for another blog post though. Regardless of what you may be using on the furniture you upcycle, the thing we ALL do is sand, loads and loads and loads of sanding!
This prep stage is hard but is always worth it in the end. When you finally get color on a piece, you see all your work pay off. So whatever you can do to make that process easier, smoother, cleaner, the better. Am I right?!
Let’s first talk power-tools…
EQUIPMENT: SurfPrep 3x4 Sander
This is not a revelation, other than, if you’re new to this biz, just buy one already. Part of the magic of these are their pads that allow the sander to conform to the shape of millwork. It can save a ton of time.
TIP: Don’t try to find SurfPrep on Amazon because they are not sold there. But you can call SurfPrep directly and ask about refurbished options. I've done that twice now. Their customer service is fantastic!
ABRASIVES: Foam, Film, Paper & Screen
For what we do, we prefer the Film and Screen Abrasives that are made for this sander.
TIP: Don’t bother trying to find alternative abrasives that fit the 3x4 SurfPrep sander either. They don’t exist.
We mostly use the 180, 200 and 400 depending upon which layer we are sanding. We usually prefer the film abrasive and use the foam backer pad that comes with the sander to provide some cushion like the foam pads do. I feel like the screen abrasive though works best in the finer sanding grits, like 400+. The foam pads are offered in 5 generalized grits, Course to Extra Fine. You should experiment with what works best.
The cushioned pads are good options for some detail areas, but it takes a lot of practice to use it well. It’s easy to sand more trim detail than you intend and accidentally change the shape of the millwork. The wood species can also play a part in this. So give yourself practice time to decide what works best for you and the type of furniture you work with most.
EQUIPMENT: Random Orbital Sanders
An orbital is a great tool as well. They move in circles but also oscillate at the same time. The oscillating action helps reduce swirl marks that can be magnified when you apply primer and color. If you want to really geek out on it, the width of the oscillation can make a difference depending upon what type of abrasive you use and surface you are sanding. Read the fine detail.
I’ve used a cheap Black and Decker for years and then 2 years ago bought a Bosch at Rockler. I also splurged on a very expensive 3M model that did not work at all. It would get very hot and develop a static shock which was….wait for it….shocking. Start cheap to moderate and then be prepared to test a few.
TIP: Do not tackle a newly rescued piece of furniture with new equipment. Get something you can test and beat up over and over. We have a piece we call Mr. Potato Head. We’ve done all sorts of things to him and he’s proven his worth over and over!
DUST COLLECTION:
Buy yourself a dust collection system or one that is a dual shop vac function. The Festool system is very good, but quite expensive. They are like Dyson for the workshop. I’ve purchased 2 of these and they are very good!
One of the things I love is that you plug your sander directly into an outlet on the shop vac. When you turn your sander on, it powers your tool and the shop vac starts to pull the dust through the sander and from the surface you are sanding. It is a very helpful feature. On the Kartcher ones in my link, don't be fooled by cheaper priced versions, they won't have the outlet on the front to power your tool. So look closely at the images and read the descriptions before you buy. Also make sure you get the tube converters in the size you need so it can hook to the dust port directly on your sander.
TIP: Watch for sales during holidays and especially Black Friday. Also check out the Amazon Outlet for good open-box deals. Literally just search for “Amazon Outlet” on Amazon. My carpenter turned me onto this. It just seemed too easy, but in fact has great deals every day.
Now, let’s dive into the human-powered tools. These are the little gems that will make your pieces and process so much better. Especially if you have any sort of arthritis like I do. These will make it easier on your finger joints.
SANDING TWIGS:
Ideal for sanding tight areas that the SurfPrep can’t get to. These usually come in multi-packs, but we cut them into thirds so we can use them multiple times. You can find variations of these on hobby sites, such as for model trains.
MICRO FINISHING BANDS:
These are small bands of sand paper that you apply to a pen-like tool. You can gradually move the band as it gets worn. These also are a game changer. The bands are a great option if you don’t use all the grits in the Sanding Strip packs. You can order bands in specific grits only.
Blicks carries these in addition to Amazon.
TUNGSTEN CARBIDE BLOCK:
Andy found this trick from watching guitar finishing videos. That process is similar to what we do. Auto painting is also a great industry resource. This tool comes in handy when you’re at the color or top coat stage and you have a drip, you don’t want to risk oversanding and end up back down to primer or you’ll have to respray color. So, this tool helps to ensure you are just taking off the meat of the drip and not any material around it. If possible, you should find a way to practice with this tool before using it on product, it is very powerful, but also a bit tricky and can do damage if not used properly.
TIP: You can learn alot about the lacquer process from watching YouTube videos from people in adjacent industries, such as guitar finishing or auto-painting.
MINI HAND SANDING BLOCKS:
These are “denibbing” tools, used on auto painting. Sometimes there is overspray still floating in the air after a spray session. By the time it lands back onto the surface you are spraying, it’s already partially dry. This is specific to lacquer since it dries so fast. Paint doesn’t always have this issue because the dry time is so long. But with lacquer you can end up with a rough surface that can feel rough to the hand, but not usually see. So these blocks help to “denib” that issue. We also use them, alternating with the titanium block for drips.
These tools are made for detail painters. They are small handheld molds made to the specific shapes of common millwork forms. You can hold your sandpaper against it to get a consistent sand on millwork details. This is sometimes a better option than the SurfPrep sander when you have really delicate areas or soft woods or even when you’re re-creating a piece of millwork with Bondo. You need to make sure you don’t oversand in these situations.
DIY MOLDS:
This is often a game-changer if nothing else is working. You can make your own molds out of thermoplastic. This stuff is amazing and reusable!
BIG KIDS SANDING BLOCKS (or DIY BLOCKS):
Big Kid Blocks are a tool a lot of furniture painters have borrowed from the auto-painting industry. They come in different materials for various levels of flex. Picture a long skinny plastic piece that curves with the hood of a car. Very useful for sanding. They come with sticky-back or hook and loop (aka velcro) attachment.
For a long time I used the Mini Detail Kit. These are amazing, but the handles are small so Andy decided that building our own was a better solution. He was able to make them to fit the SurfPrep papers and with the same hook & loop attachment. Now the grips are bigger and much easier to work with for hours on end.
TIP: Click here for the parts list to make your own sanding blocks. (NEED CONTENT)
You can go to any plastic supply store (like TAP plastics) for the plastic and the plastic cement. We rummage through the scrap bin for our plastic. These pieces are sold by the pound and are often scratched or an odd color which does not matter for this purpose. We get our hook and loop from amazon:
TIP: The adhesive on this product is going to take a beating. For best results, it should sit for 72 hours between adhering it and putting it into use. (We did this and have never had a failure.)
All in all we were able to make 20 sanding blocks for about $30.
So I hope this is helpful. If you have any specific questions about how we use these or do anything else, please don’t hesitate to contact me. I hope to encourage more people to transform heirlooms into #rheirlooms. Whether you’re working on your own family piece or one you’ve found at a garage sale, the effort always pays off when you’re done. Using a few smart tools can make the difference so that the next generations will cherish that heirloom you transformed with your own hands, into a #rheirloom.